- Call Us: +91-9925047484
- Email: hpvalves@gmail.com
Safety Valve
Product Categories
- Safety Relief Valve
- Pressure Reducing Valve
- Knife Gate Valve
- Control Valve
- Piston Valve
- Blow down Valve
- Moisture Separator
- Check Valve
- Ball Valve
- Diaphragm Valve
- Gate Valve
- Poppet Valve
- Globe Valve
- Butterfly Valve
- Strainer ('Y'/'T'/Basket)
- Forged Steel Valve
- Cryogenic Valve
- Pressure Seal Valve
- Pinch Valve
A Safety valve which automatically discharges steam, gases or vapours so as to prevent a predetermined safe pressure being exceeded. Such valves usually have a rapid opening.
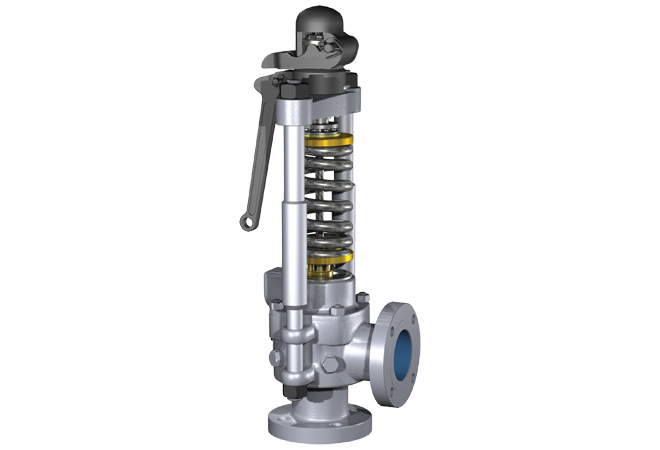
A valve which automatically discharges liquid so as to prevent a predetermined safe pressure being exceeded. Here the lift is proportional to the increase in pressure above the set pressure.
The working pressure of vessel is the pressure in pounds per square inch gauge or [Kg/cm2 (g)], to which the vessel is usually subjected in service. In process vessel the working pressure should be less by 10% or 25 psig than the maximum allowable working pressure.
The inlet gauge pressure of a Safety Relief Valve at which the valve pops or starts discharging.
Pressure increase over the set pressure of the relief valve is called over - pressure; usually the over-pressure will be either 10% or 25% of the set pressure.
The gauge pressure on the discharge side of a Relief Valve.
Pressure increase over the maximum allowable working pressure of the vessel during discharge through the pressure relief valve expressed as a per cent of that pressure or pounds per square inch is called accumulation.
Blow down is the difference between set pressure and the Re-seating pressure of Safety Relief Valve expressed as percentage of the set pressure or pounds per square inch.
It is necessary to calculate the orifice area to relieve the predetermined quantity of liquid or vapor. Once the orifice area is determined it is very easy to get the required size of the valve from the manufacturer's list.
Higher size valve can be given as per party’s requirement considering the capacity and orifice area.
The purpose of the lifting mechanism is to open the valve, when the pressure under the valve disc is lower than the set pressure. These mechanisms are made in two basic types, plain lever and packed lever.
This lever assembly is not pressure tight. This type of lever can be used where the vapor discharging from an open valve is permissible. For Example – steam.
As indicated by the name, this lifting lever assembly is packed around the lever shaft, so that leakage will not occur around the upper part of the valve when the valve is open or when back pressure is present. The packed lifting lever should be used when positive protection against leakage is required. For Example – Liquid or Gas
In most cases pressure relief valve manufacturers prefer to verify the sizing of their products in order for the valve to be sized and recommendation made, the following information must be supplied.
- Material of Construction.
- Set pressure in psig or Kg/cm2 (g).
- Maximum inlet temperature.
- Allowable over-pressure.
- Service-Specify either the media to be handled or the following physical properties or both.
- Liquids-Specific gravity (Water = 1)
- Gases-Specific gravity (Air=1)
- Vapors-Molecular weight (mixture of vapors. The average molecular weight)
- Back pressure, if any.
- Required capacity.
- Type of End-connections.
- Preferred inlet size.
Modern plants demand highly efficient well designed meticulously manufactured safety valves. Our safety valve is capable of dealing with the pressure and temperature normally encountered in the steam process and compressed air. The materials used are as per I.B.R.
Heat and corrosion resistant high chrome alloy trim. Self aligning flat faced valve, disc and seat remain pressure tight. Carefully lapped flat faces of valve and seat to optical precision, guarantee pressure tightness.
Top guided to ensure high discharge capacities. Thus, ensuring the use of a valve of the minimum size for the given duties. Materials used are selected to suit service conditions.
More refinement and complication of design is necessary to meet needs for leak tightness, capacity achievement and low blow down. The severe demands on the conventional safety valve resulted in the manufacture of H.P. Valves Make Safety Relief Valve. The designs of two control rings meet with the ASME Code Requirement for high pressure safety relief valves.
In the closed position, the nozzle or lower adjusting ring is set with its upper edge slightly above the seat. The result is a confinement of the escaping steam and a forcing upward of the disc. Once this occurs, the steam can move outward and be reversed by the upper adjusting rings, developing added lift force.
If the upper adjusting ring is lowered, the steam must turn further than if the ring were high. Reacting effect on the disc is greater when the ring is low, so that the pressure must drop further below the set pressure before the spring can close the valve. In other words, the blow down will be higher when the upper ring is low. Conversely, raising the upper adjusting ring reduces the blow down.
By using this reaction effect principle results in maximum capacity, precise control, short blow down, smooth operation and long life of valve seat.
The simple design guarantees that tightness over long period is ensures in addition the operation is positive and accurate with the low blow down.
A frequent cause of faulty operation is eliminated in the H.P.Valves design by the use of a disc-guide which is entirely removed from the nozzle. Guide webs or wings below the disc are in direct contact with the fluid. Owing to the necessarily close fit, they sometimes stick, either from expansion when hot or from scale or boiler compound deposits. Moreover, guides or wings within the nozzle occupy a very valuable area of discharge and cause eddy currents which reduce the capacity and cut the seating surface.
In the H.P.Make valves the guide is entirely above the disc and the guides are free from temperature distortion.
The two ring control design eliminates the compromise setting inevitably associated with designs of single ring control. The nozzle ring is adjustable to give a sharp opening pop and positive closing.
The guide ring adjustment enables high lift discharge to be attained but not at the expense of prolonged blow down. A blow down of 5 percent is readily achieved. The design permits the valve Disc to attain a lift to ensure full nozzle discharge with an accumulation or over pressure as low as 5 percent of the set pressure.
In ordinary diction the terms "safety valve" and "relief valve" are frequently used interchangeably. This is satisfactory to the extent that both safety valves and relief valves of the spring-loaded type are similar in external appearance and both serve the board general purpose of limiting fluid (liquid or gaseous) pressures by discharging some of the pressurized liquid or gas. Some authorities restrict "Safety valve" to those installed on boilers, super heaters and fired vessels-all others being classified as relief valves. We prefer, however, to define them briefly as follows:
Safety valves are for use with gases-which include air and steam. Their design always includes a huddling chamber which utilizes the expansion forces of these gases to affect quick opening (popping) and closing down actions. The difference between the opening and closing pressures is termed “blow down”; and for steam safety valves blow down limitations are carefully stated in the A.S.M.E. Power Boiler Code.
Relief valves are normally used for liquid service, although safety valves may be so used. Ordinarily relief valves do not have an accentuated huddling chamber Nor a regulator ring for varying or adjusting blow down. They therefore operate with a relatively lazy motion, slowly opening as pressure increases and slowly closing as pressure decreases. Such relieving action affords suitable protection for vessels or systems where there is no need for instantaneous release of large volumes, and where sufficient leeway is provided between the design pressure and the operating pressure in the system.
- All valves are furnished with plain bolted cap unless otherwise specified.
- For set pressures under 10 psig (0.7 kg/cm sq) close bonnet and close cap will be provided.
- ASME Section VIII Boiler and Pressure Vessel Code requires that Pressure Relief Valves, have lifting levers installed for hot water service over 140 F (600 C).
- Corrosive, low and high temperature materials ANSI class 150 inlet flange and open yoke design are available on application details.
- Complete bill of materials, cross-sectional view and dimensions can be provided on request.
- All flanges are furnished serrated, unless otherwise as per requirement.